”LEAN hjälper till att förbättra effektiviteten och eliminera slöseri”
Koncept att integrera & utveckla
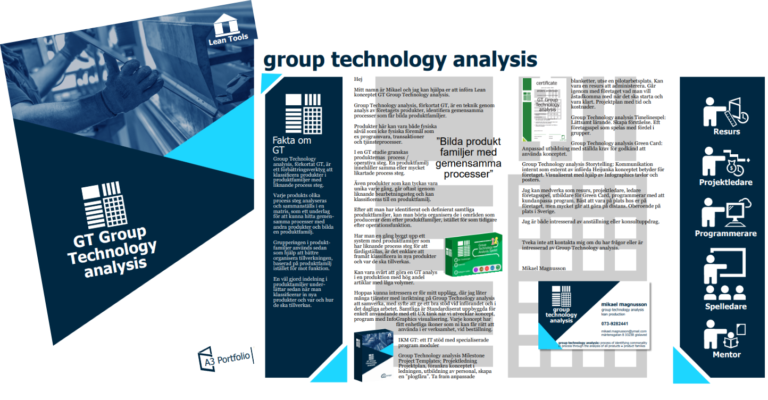
Vad innebär konceptet GT Group Technology analysis?
Group Technology analysis är en teknik att analysera och kategorisera företagets produkter, identifiera gemensamma processer som får bilda produktfamiljer. Produkter här kan vara både fysiska såväl som icke fysiska föremål som ex programvara, transaktioner och tjänsteprocesser. I en GT studie granskas produkternas process / operativa steg. En produktfamilj innehåller samma eller mycket likartade process steg. Även produkter som kan tyckas vara unika varje gång, går oftast igenom liknande bearbetningssteg och kan klassificeras till en produktfamilj.
Group Technology innebär att delar med liknande geometri, material, tillverkningsprocesser eller funktioner identifieras och grupperas i så kallade ”part families”. Dessa delar tillverkas sedan i en gemensam produktionscell, vilket minskar behovet av att transportera delar mellan olika maskiner och avdelningar.
Group Technology (GT) är en tillverkningsfilosofi inom Lean som organiserar produktionen genom att gruppera liknande delar och processer för att öka effektiviteten och minska kostnaderna.
Fördelar
Här är några av de främsta fördelarna med att använda Lean Group Technology (GT) analys. Genom att implementera Lean Group Technology analys kan organisationen dra nytta av fördelar och skapa en mer effektiv och konkurrenskraftig produktionsmiljö. Organisationen kan uppnå betydande förbättringar i effektivitet, kvalitet och kostnadseffektivitet.
- Ökad produktivitet: Genom att gruppera liknande delar och processer kan produktionen standardiseras och effektiviseras, vilket leder till högre produktivitet.
- Minskade ledtider: Eftersom delar tillverkas i en gemensam produktionscell, minskar tiden det tar att flytta delar mellan olika maskiner och avdelningar.
- Förbättrad kvalitet: Standardisering av processer och arbetsmoment leder till en jämnare och högre kvalitet på slutprodukterna.
- Minskade kostnader: Genom att minska slöseri och ineffektivitet kan tillverkningskostnaderna reduceras.
- Flexibilitet: GT gör det möjligt att snabbt anpassa produktionen till förändrade krav och förutsättningar genom att omorganisera part families och produktionsceller.
- Bättre resursutnyttjande: Genom att gruppera liknande delar kan maskiner och arbetsstationer användas mer effektivt, vilket minskar behovet av överkapacitet.
- Förbättrad planering och schemaläggning: Med en tydlig översikt över vilka delar som tillverkas i vilka celler blir det enklare att planera och schemalägga produktionen.
- Minskad lagerhållning: Eftersom produktionen blir mer effektiv och standardiserad, kan behovet av att hålla stora lager minskas.
- Förbättrad arbetsmiljö: Genom att skapa produktionsceller där operatörerna arbetar med liknande uppgifter kan arbetsmiljön förbättras och arbetsbelastningen bli mer balanserad.
- Stöd för kontinuerlig förbättring: GT-analys uppmuntrar till en kultur av kontinuerlig förbättring genom att ständigt identifiera och eliminera ineffektivitet.
- Förbättrad lagerhantering: Genom att gruppera liknande delar och processer kan du minska behovet av stora lager, vilket leder till lägre lagerhållningskostnader och bättre lageromsättning.
- Minskad omställningstid: Eftersom liknande delar tillverkas i samma produktionscell, kan omställningstiden mellan olika produktionskörningar minskas, vilket ökar maskinutnyttjandet.
- Förbättrad arbetsflöde: GT hjälper till att skapa ett mer logiskt och smidigt arbetsflöde genom att minska onödiga rörelser och transporter inom produktionen.
- Ökad flexibilitet i produktionen: Genom att ha produktionsceller som kan hantera flera olika delar inom samma familj, kan produktionen snabbt anpassas till förändrade kundbehov och marknadskrav.
- Bättre utnyttjande av maskiner och utrustning: Genom att gruppera liknande delar kan maskiner och utrustning användas mer effektivt, vilket minskar behovet av överkapacitet och investeringar i nya maskiner.
- Förbättrad produktutveckling: GT kan underlätta produktutvecklingsprocessen genom att standardisera tillverkningsprocesser och minska komplexiteten i produktionen.
- Ökad konkurrenskraft: Genom att förbättra effektiviteten och kvaliteten i produktionen kan din organisation bli mer konkurrenskraftig på marknaden.
- Stöd för hållbarhet: Genom att minska slöseri och optimera resursanvändningen kan GT bidra till en mer hållbar produktion med mindre miljöpåverkan.
- Förbättrad kundnöjdhet: Genom att leverera produkter snabbare och med högre kvalitet kan du öka kundnöjdheten och bygga starkare kundrelationer.
- Stöd för digitalisering: GT kan integreras med digitala verktyg och system för att ytterligare förbättra effektiviteten och spårbarheten i produktionen.
Nackdelar
Här är några potentiella nackdelar med att använda Lean Group Technology (GT) analys. Genom att vara medveten om potentiella nackdelar kan man bättre förbereda dig för att hantera dem och maximera fördelarna med att använda Lean Group Technology analys.
- Hög initial kostnad: Implementeringen av GT kan kräva betydande investeringar i tid och resurser för att analysera och omstrukturera produktionsprocesserna.
- Komplexitet i analysen: Att identifiera och gruppera delar i part families kan vara en komplex och tidskrävande process, särskilt i företag med ett stort antal olika produkter.
- Behov av kontinuerlig uppdatering: För att GT ska vara effektivt måste data och produktionsceller kontinuerligt uppdateras för att återspegla förändringar i produktsortiment och tillverkningsprocesser.
- Risk för överstandardisering: Överdriven standardisering kan leda till minskad flexibilitet och innovation, eftersom fokus ligger på att följa etablerade processer snarare än att utforska nya metoder.
- Motstånd mot förändring: Implementeringen av GT kan möta motstånd från medarbetare som är vana vid befintliga arbetsmetoder och kan vara ovilliga att anpassa sig till nya processer.
- Begränsad användbarhet i vissa miljöer: GT är mest effektivt i tillverkningsmiljöer med hög volym och låg variation. I miljöer med hög variation och låg volym kan det vara svårare att tillämpa GT effektivt.
- Kräver omfattande utbildning: För att säkerställa att alla medarbetare förstår och kan tillämpa GT korrekt krävs omfattande utbildning och träning, vilket kan vara tidskrävande och kostsamt.
Steg-för-steg guide
Genom att följa steg kan man effektivt implementera Lean Group Technology analys i din organisation och uppnå ökad effektivitet, minskade kostnader och förbättrad kvalitet i din produktion.
Steg 1: Identifiera Part Families
- Samla in data: Börja med att samla in detaljerad information om alla delar som tillverkas i din produktion. Detta inkluderar geometri, material, tillverkningsprocesser och funktioner.
- Klassificera delar: Använd denna data för att identifiera och gruppera delar med liknande egenskaper i så kallade ”part families”. Detta kan göras manuellt eller med hjälp av programvara för gruppteknologi.
Steg 2: Skapa Produktionsceller
- Designa celler: Organisera maskiner och arbetsstationer i produktionsceller som är dedikerade till specifika part families. Varje cell bör vara utrustad för att hantera alla nödvändiga processer för de delar som tillverkas där.
- Layoutoptimering: Placera maskiner och arbetsstationer i en layout som minimerar transport och hantering av delar inom cellen.
Steg 3: Standardisera Processer
- Utveckla standarder: Skapa standardiserade arbetsmetoder och processer för varje produktionscell. Detta inkluderar arbetsinstruktioner, kvalitetskontroller och underhållsrutiner.
- Utbilda personal: Säkerställ att all personal är utbildad i de nya standarderna och förstår hur de ska tillämpas i det dagliga arbetet.
Steg 4: Implementera och Övervaka
- Genomför förändringar: Implementera de nya produktionscellerna och standardiserade processerna i din produktion.
- Övervaka prestanda: Använd kontinuerlig övervakning och analys för att följa upp prestanda och identifiera eventuella problem eller förbättringsmöjligheter.
Steg 5: Kontinuerlig Förbättring
- Analysera data: Samla in och analysera data från produktionscellerna för att identifiera ineffektivitet och flaskhalsar.
- Justera och förbättra: Använd insikterna från analysen för att justera processer och layout, samt implementera förbättringar kontinuerligt.
GT Blankett
En blankett för Lean Group Technology (GT) analys är vanligtvis organiserad för att systematiskt samla in och analysera data om delar och processer. Genom att använda en sådan blankett kan en organisation systematiskt samla in och analysera data för att identifiera ineffektivitet och förbättringsmöjligheter i produktionsprocessen. Här är en översikt över hur en sådan blankett kan vara strukturerad:
1. Delinformation
- Delnummer: Unikt identifieringsnummer för varje del.
- Delnamn: Beskrivande namn på delen.
- Material: Typ av material som används för delen.
- Geometri: Beskrivning av delens form och dimensioner.
2. Tillverkningsprocesser
- Processsteg: Lista över alla tillverkningssteg som delen genomgår.
- Maskiner: Maskiner som används i varje steg.
- Bearbetningstid: Tidsåtgång för varje tillverkningssteg.
- Inställningstid: Tid som krävs för att ställa in maskiner för varje steg.
3. Klassificering av delar
- Part Family: Gruppnamn för delar med liknande egenskaper och tillverkningsprocesser.
- Kriterier för gruppering: Specifika kriterier som används för att gruppera delar, såsom material, geometri eller tillverkningsprocesser.
4. Produktionsceller
- Cellnamn: Namn på produktionscellen där delen tillverkas.
- Maskinlayout: Beskrivning av maskinernas placering inom cellen.
- Arbetsstationer: Specifika arbetsstationer inom cellen och deras funktioner.
5. Standardiserade processer
- Arbetsinstruktioner: Detaljerade instruktioner för varje arbetsmoment.
- Kvalitetskontroller: Beskrivning av kvalitetskontroller som ska utföras i varje steg.
- Underhållsrutiner: Rutiner för underhåll av maskiner och utrustning.
6. Uppföljning och förbättring
- Prestandamått: Nyckeltal för att mäta effektiviteten i produktionscellen, såsom cykeltid, produktionsvolym och kvalitetsnivå.
- Problem och åtgärder: Dokumentation av identifierade problem och vidtagna åtgärder för att lösa dem.
- Förbättringsförslag: Förslag på förbättringar baserade på analysen av data.
Organisation
En organisation som arbetar med Lean Group Technology (GT) analys är strukturerad för att maximera effektiviteten och minimera slöseri genom att gruppera liknande delar och processer.
Genom att integrera dessa element kan en organisation effektivt använda Lean Group Technology analys för att förbättra sina processer och skapa en mer balanserad och produktiv arbetsmiljö. Här är några nyckelelement som kännetecknar en sådan organisation:
- Lean-kultur: Organisationen har en stark Lean-kultur där alla medarbetare är engagerade i att identifiera och eliminera slöseri. Detta innebär att ständigt söka efter sätt att förbättra processer och arbetsflöden.
- Tvärfunktionella team: Team består ofta av medlemmar från olika avdelningar och funktioner. Detta främjar samarbete och gör det lättare att identifiera och lösa problem som påverkar flera delar av organisationen.
- Visuell hantering: GT-analys är en del av en bredare strategi för visuell hantering. Andra verktyg som kan användas inkluderar Kanban-tavlor, 5S-metoder och värdeflödesanalyser. Dessa verktyg hjälper till att göra arbetsflöden och problem synliga för alla medarbetare.
- Kontinuerlig utbildning och träning: Medarbetarna får regelbunden utbildning i Lean-principer och verktyg, inklusive hur man använder och tolkar GT-analys. Detta säkerställer att alla har den kunskap som krävs för att bidra till förbättringsarbetet.
- Data-driven beslutsfattande: Beslut baseras på noggrann analys av data som samlas in från GT-analys och andra källor. Detta hjälper till att säkerställa att förbättringar är baserade på fakta snarare än antaganden.
- Stödjande ledarskap: Ledarskapet i organisationen är engagerat i Lean-principer och stödjer aktivt medarbetarnas förbättringsinitiativ. Ledare fungerar ofta som coacher och mentorer, vilket hjälper teamen att nå sina mål.
- Fokus på kundvärde: Allt arbete och alla förbättringar är inriktade på att skapa värde för kunden. Detta innebär att ständigt fråga sig hur varje arbetsmoment bidrar till att möta kundens behov och förväntningar.
- Regelbunden uppföljning och justering: Organisationen har rutiner för regelbunden uppföljning av arbetsflöden och resultat. GT-analys uppdateras kontinuerligt för att återspegla aktuella förhållanden och identifiera nya förbättringsmöjligheter.
En organisation som arbetar med Lean Group Technology (GT) analys består ofta av flera olika roller för att säkerställa en effektiv och balanserad produktionsprocess. Genom att ha dessa roller i teamet kan en organisation effektivt använda Lean Group Technology analys för att förbättra sina produktionsprocesser och skapa en mer balanserad och produktiv arbetsmiljö. Här är några av de vanligaste befattningarna:
- Lean Manager: Lean-managern ansvarar för att implementera och övervaka Lean-principer inom organisationen. De ser till att GT-analysen används korrekt och att teamet följer Lean-metodiken för kontinuerlig förbättring.
- Produktionschef: Produktionschefen övervakar hela produktionsprocessen och arbetar nära Lean-managern för att identifiera och lösa flaskhalsar och ineffektivitet. De använder GT-analysen för att balansera arbetsbelastningen mellan olika operatörer och steg i processen.
- Teamledare: Teamledaren ansvarar för att leda och stödja operatörerna i deras dagliga arbete. De använder GT-analysen för att fördela arbetsuppgifter och säkerställa att alla operatörer har en jämn arbetsbelastning.
- Operatörer: Operatörerna är de som utför de faktiska arbetsmomenten i produktionsprocessen. De bidrar med insikter om hur lång tid olika moment tar och hjälper till att identifiera ineffektivitet och förbättringsmöjligheter.
- Kvalitetsansvarig: Den kvalitetsansvarige övervakar att produkterna uppfyller företagets kvalitetsstandarder. De använder GT-analysen för att säkerställa att kvalitetskontroller integreras effektivt i produktionsprocessen utan att skapa onödiga flaskhalsar.
- Processingenjör: Processingenjören analyserar och optimerar produktionsprocesserna. De använder data från GT-analysen för att identifiera och implementera tekniska förbättringar som kan öka effektiviteten och minska slöseri.
- HR-specialist: HR-specialisten arbetar med att säkerställa att personalen har rätt utbildning och kompetens för att utföra sina arbetsuppgifter effektivt. De kan också använda GT-analysen för att identifiera behov av ytterligare utbildning eller omfördelning av arbetsuppgifter.
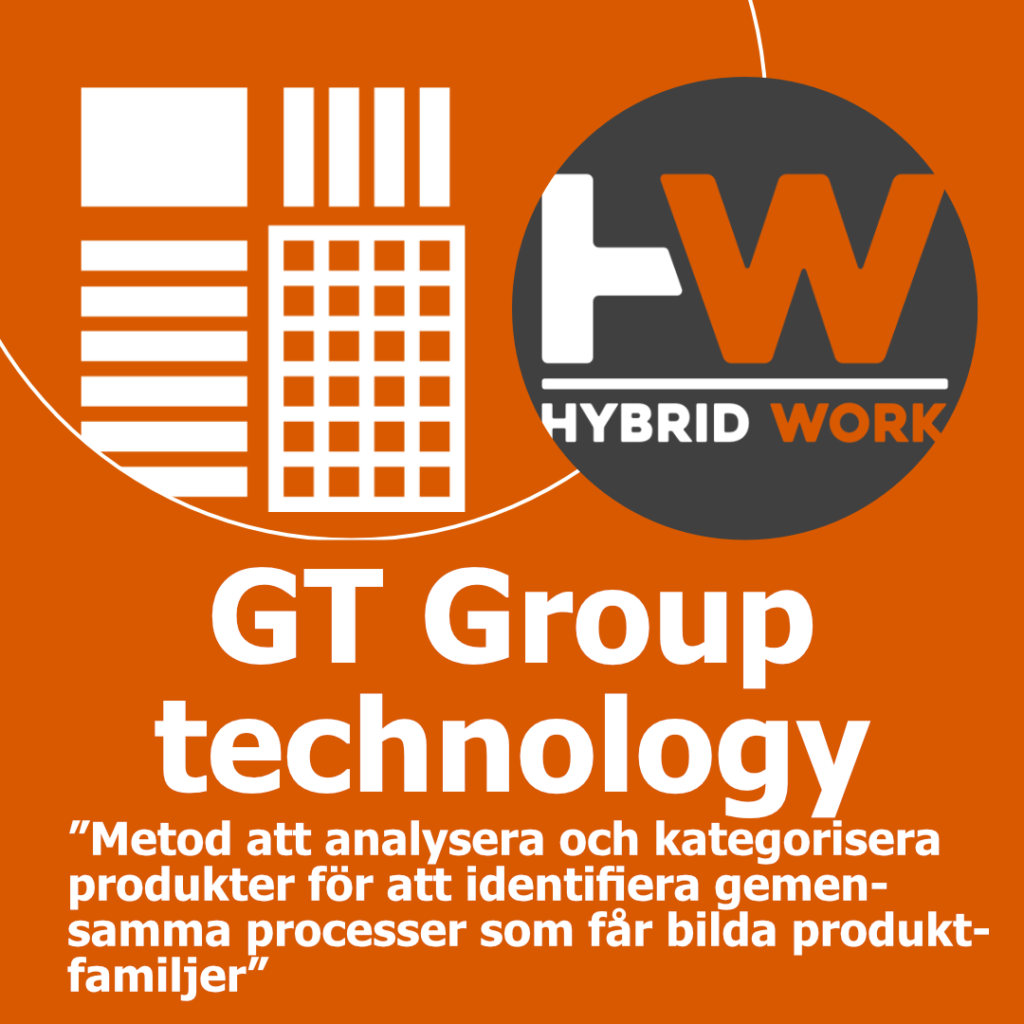
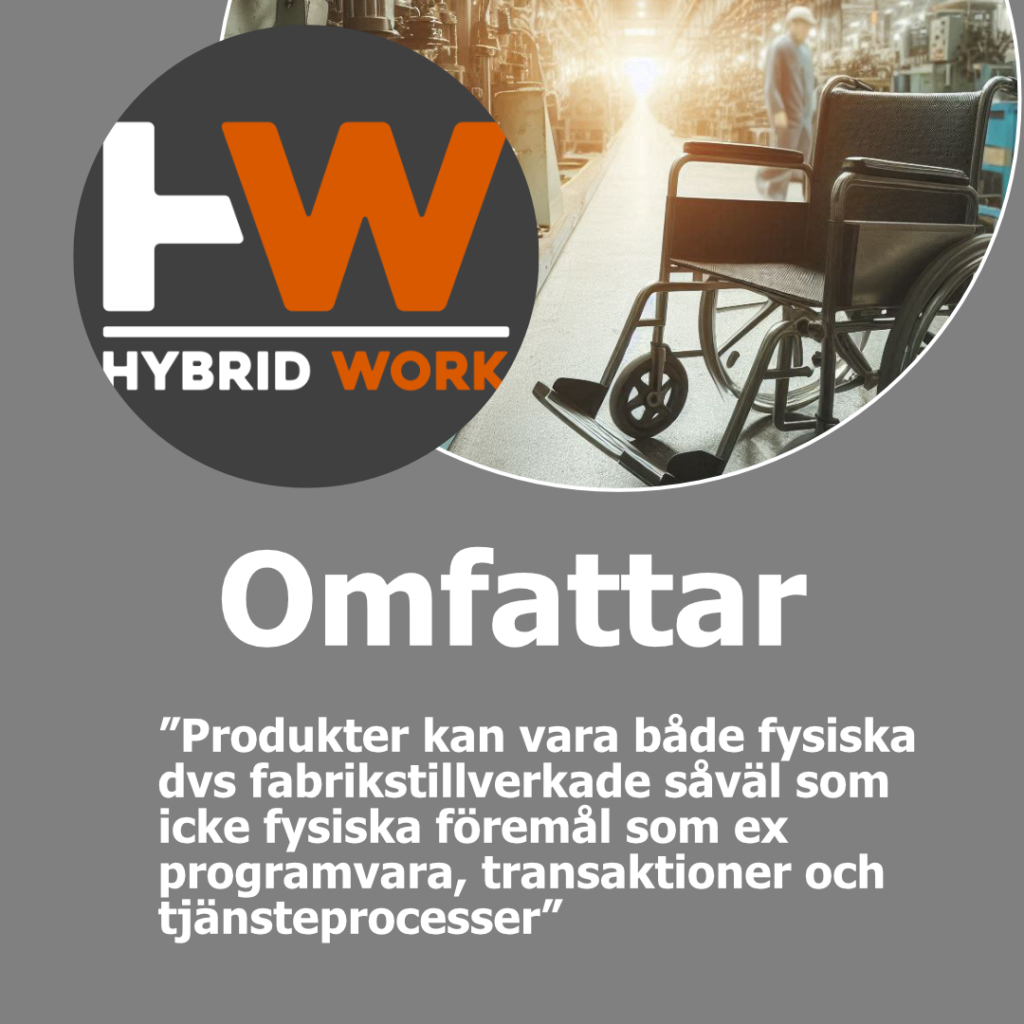
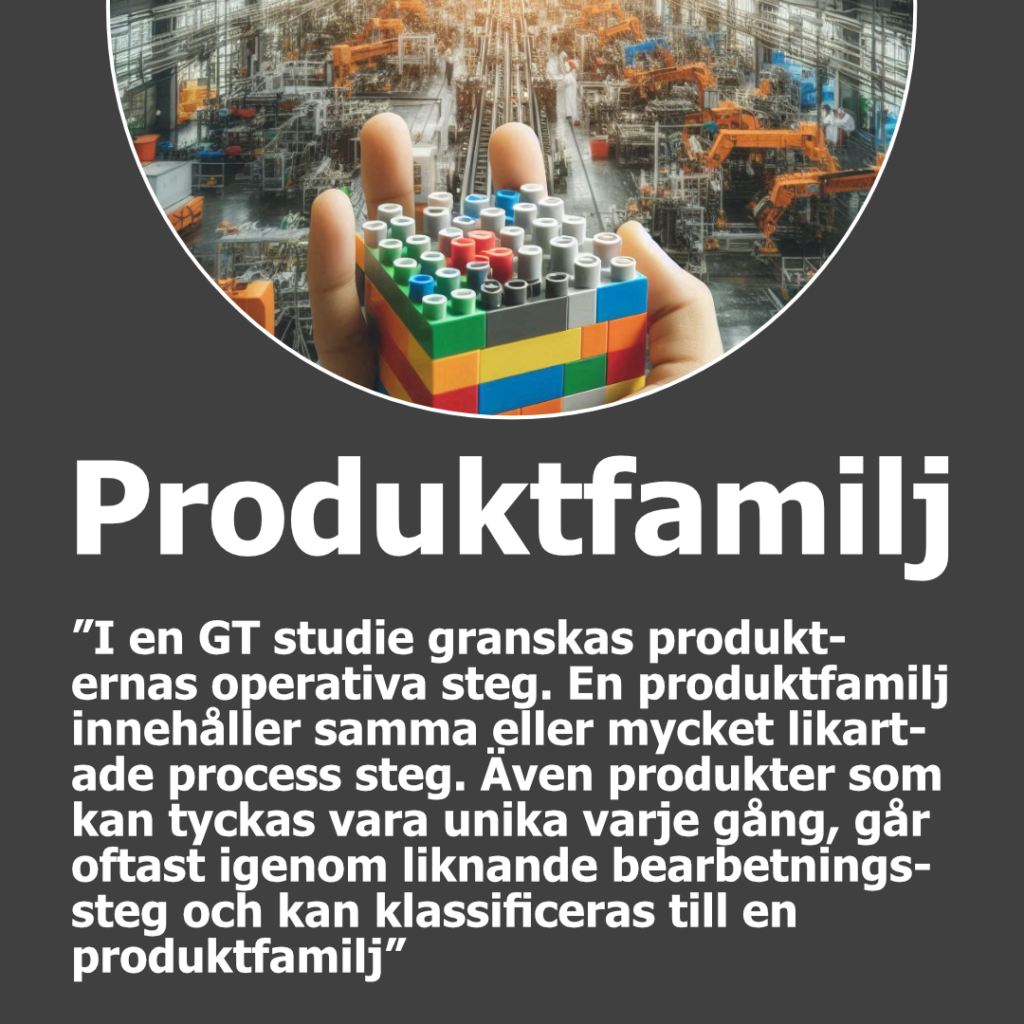
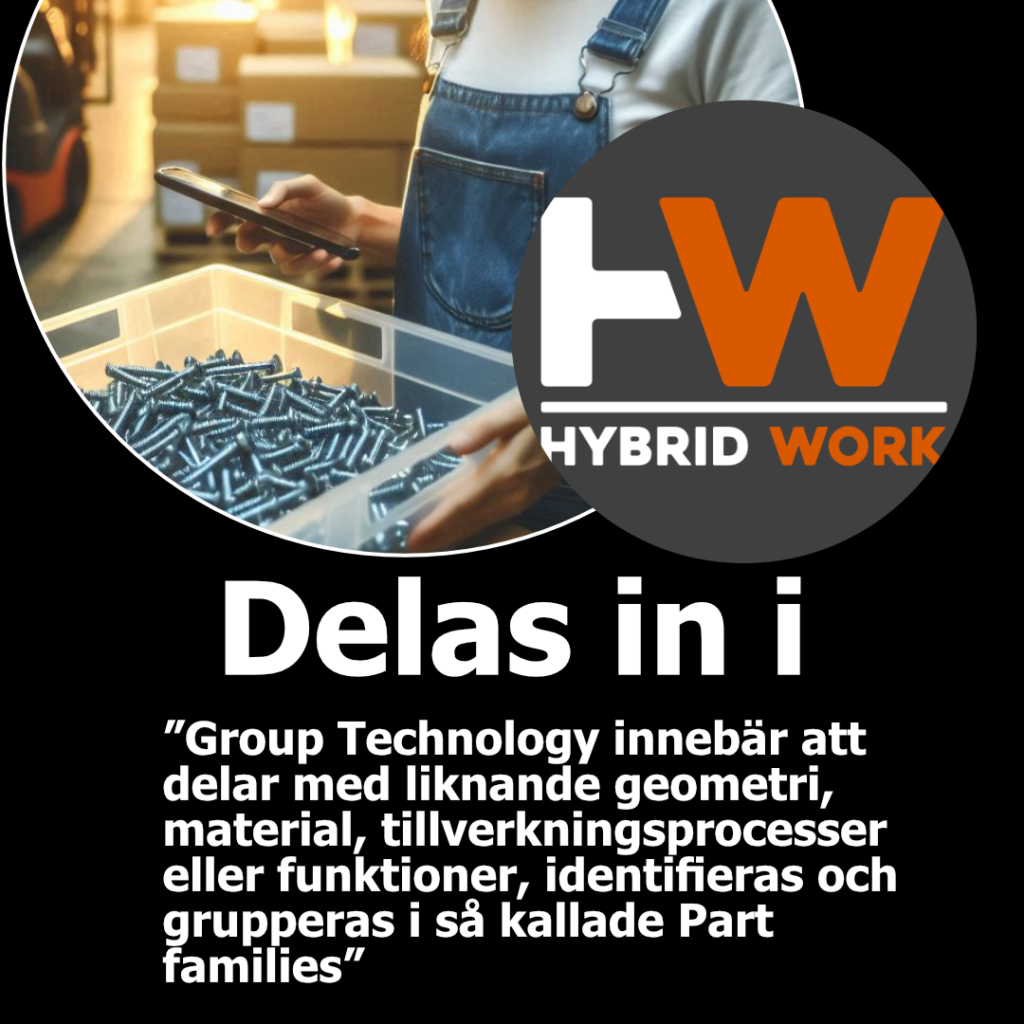
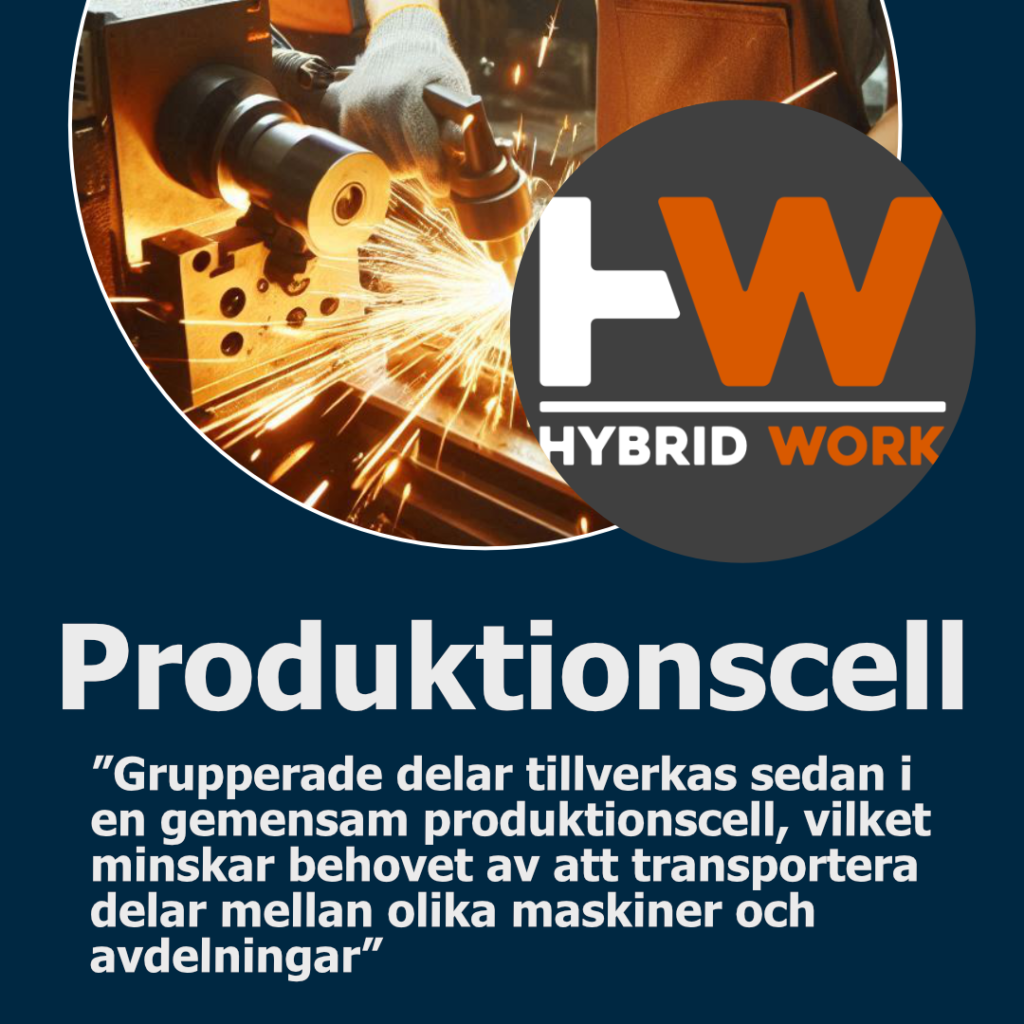
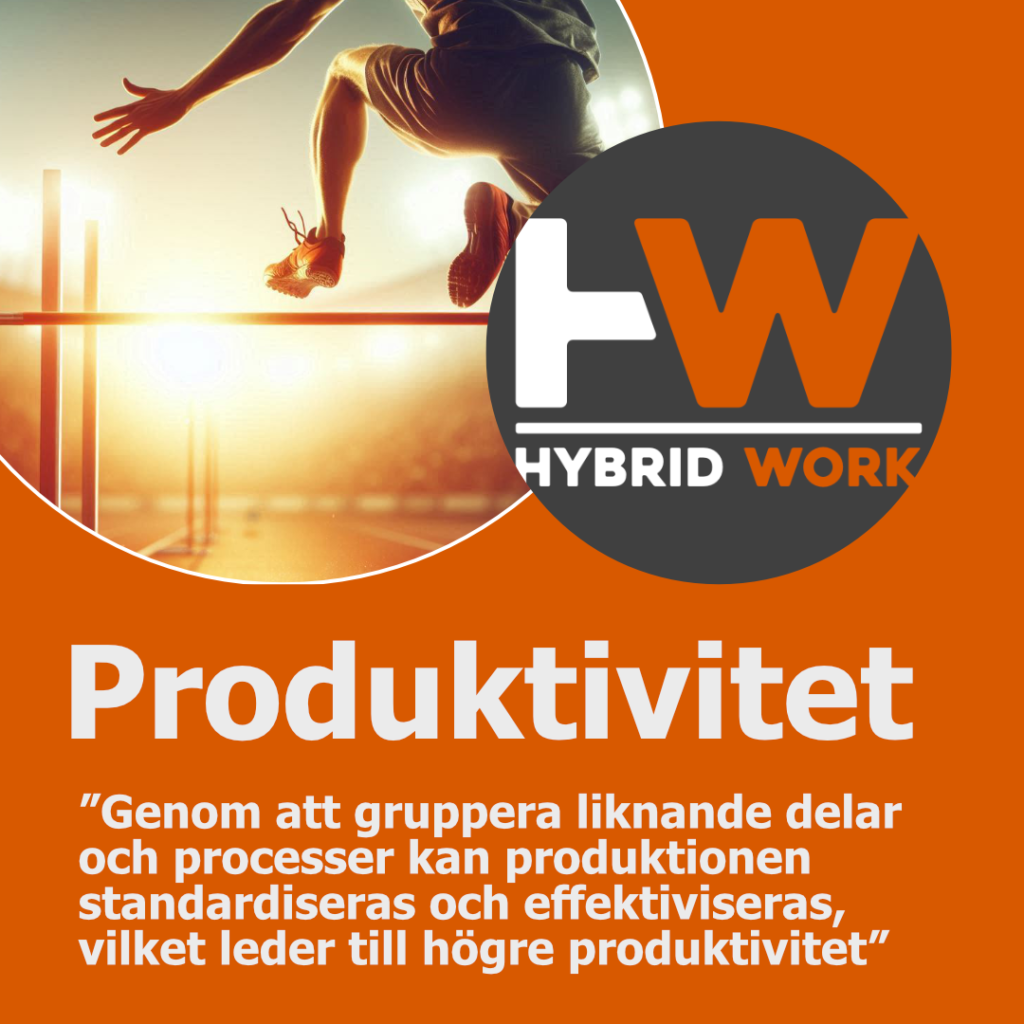
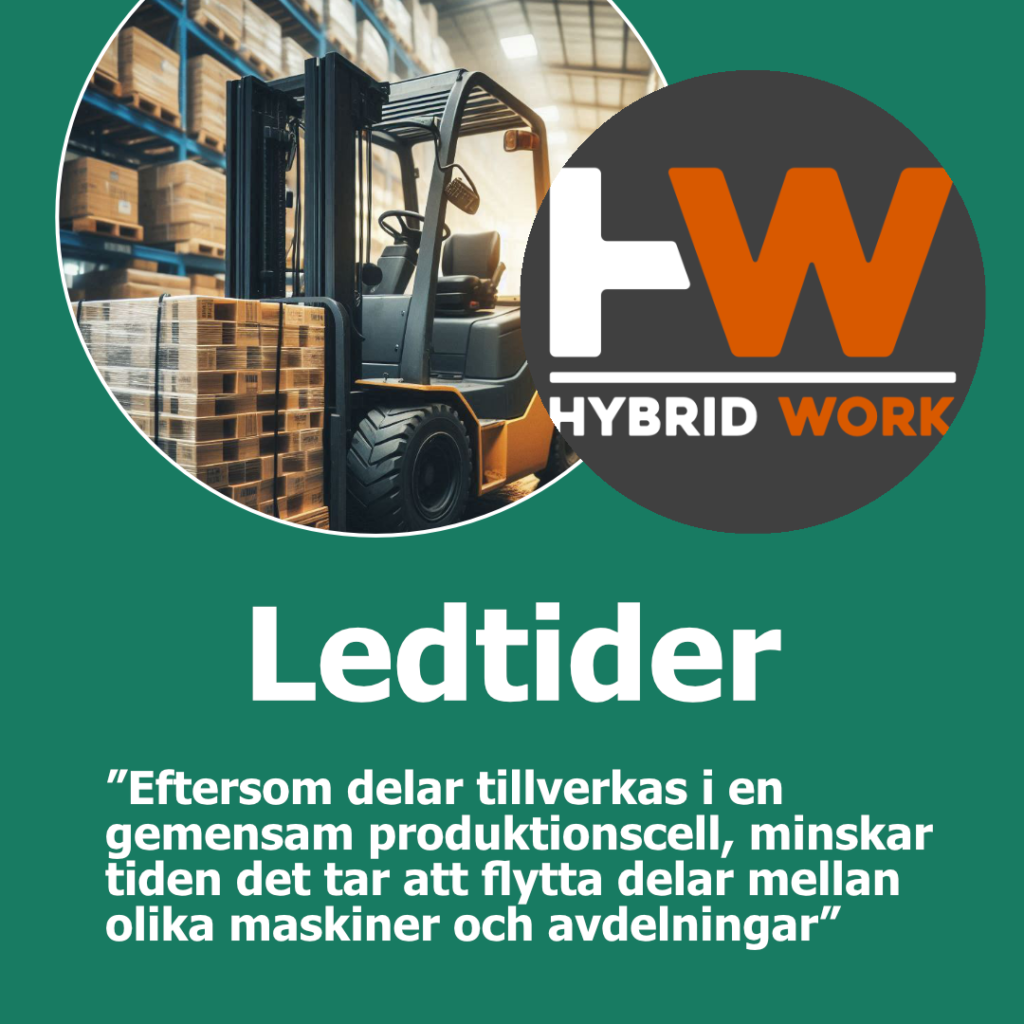
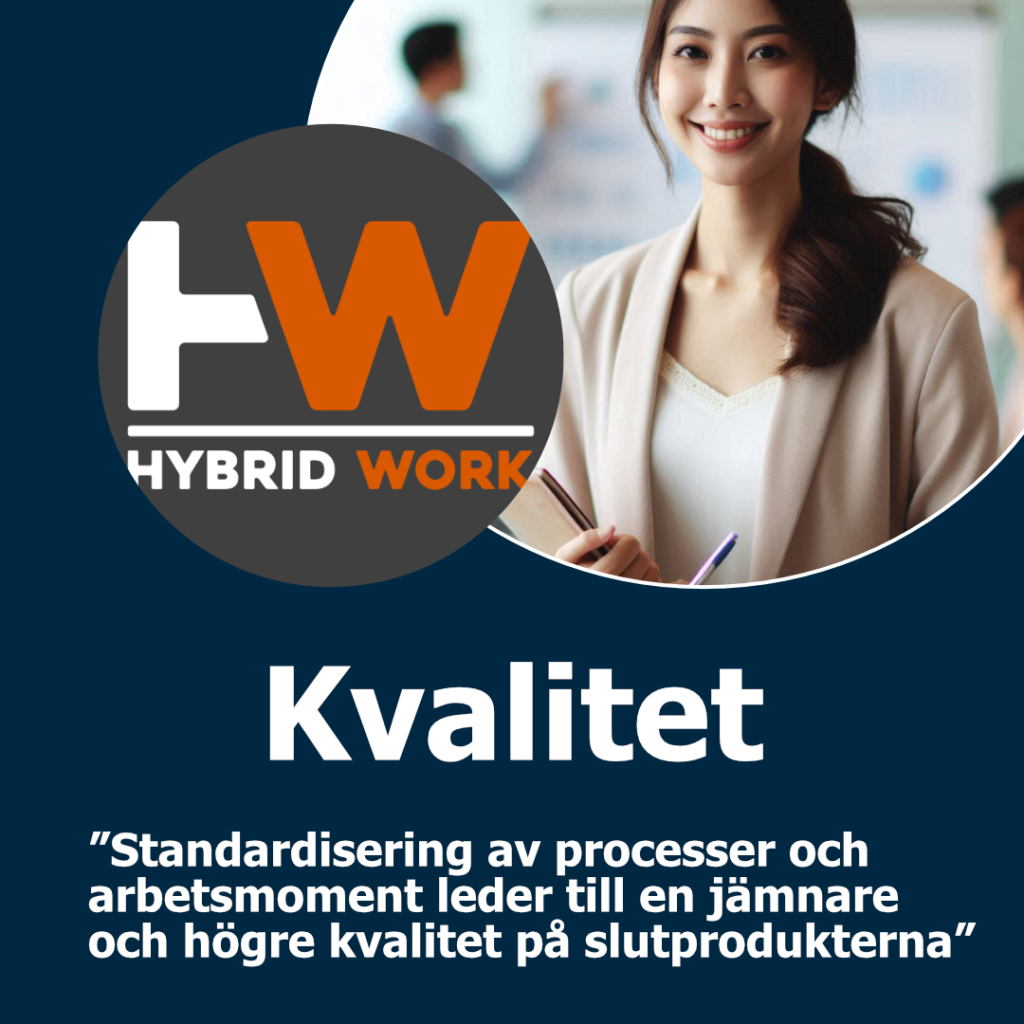
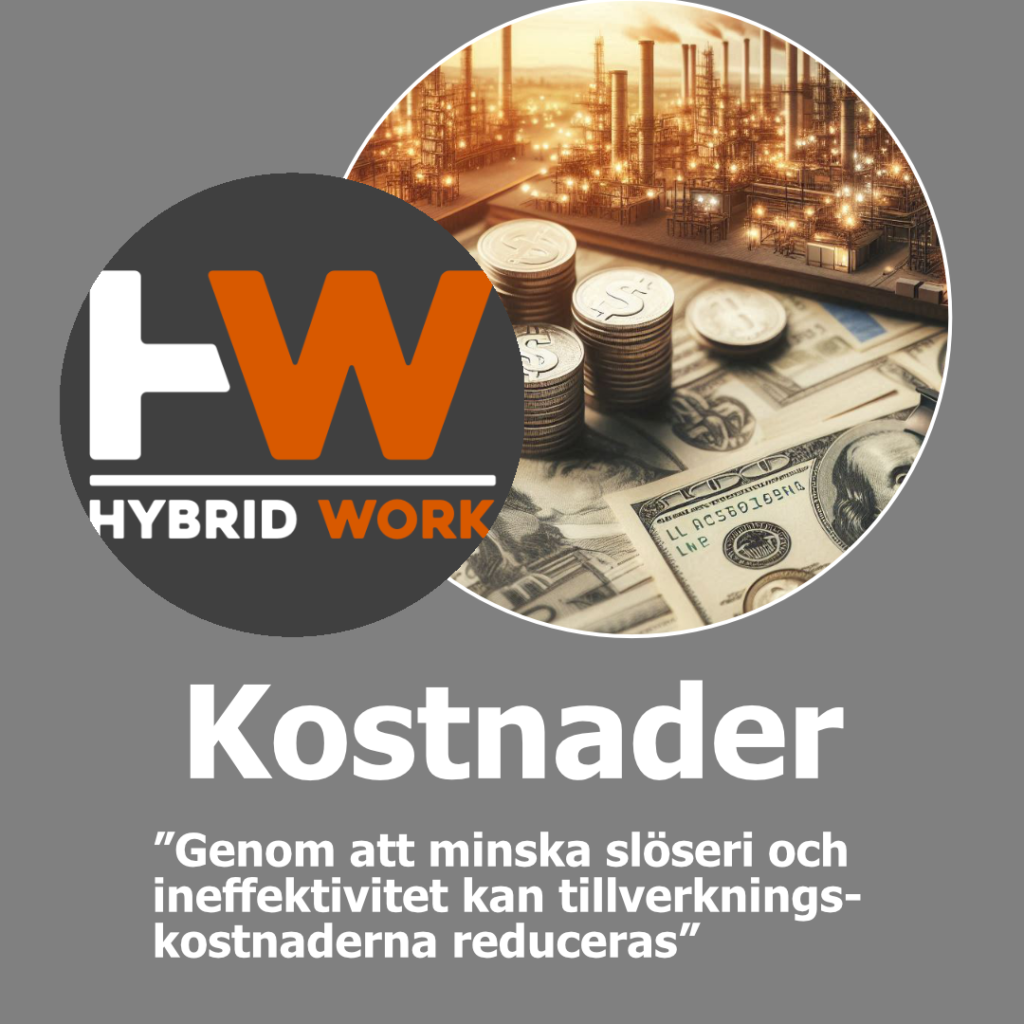
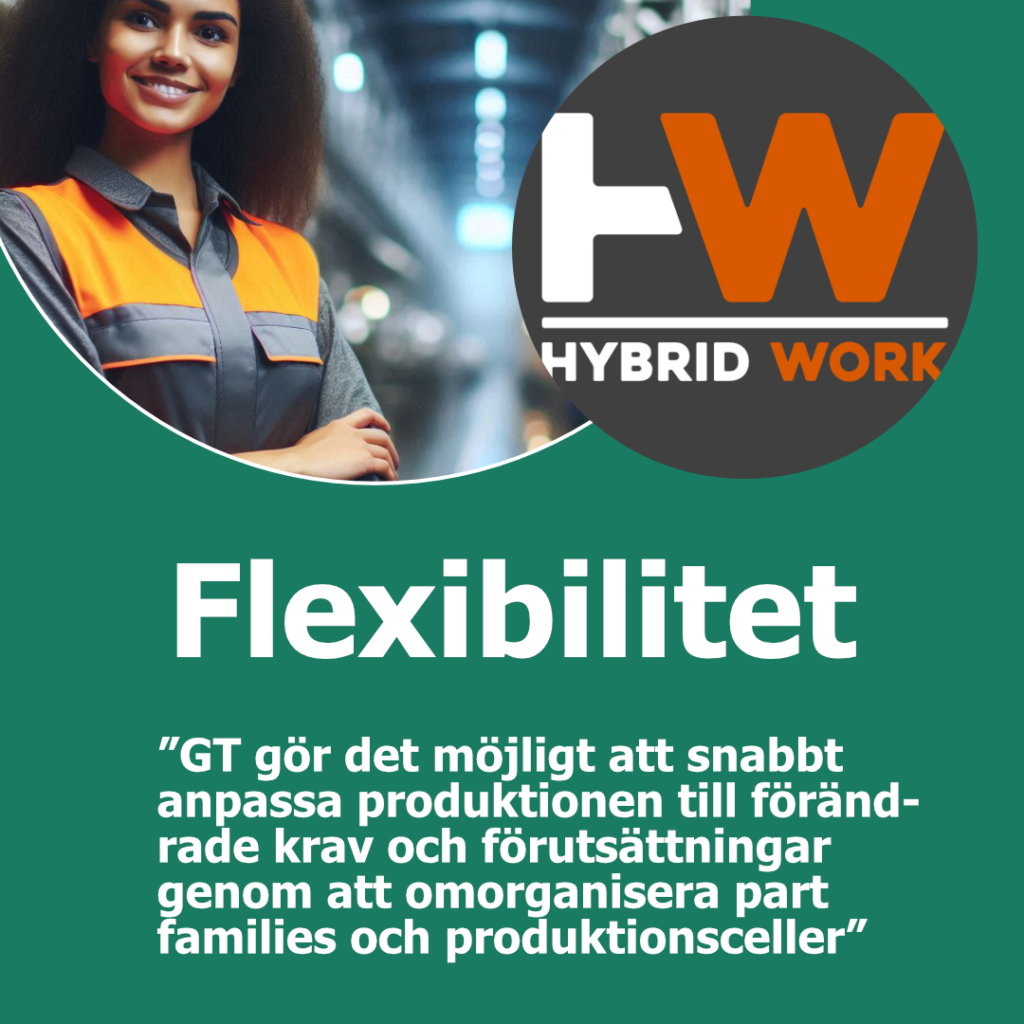
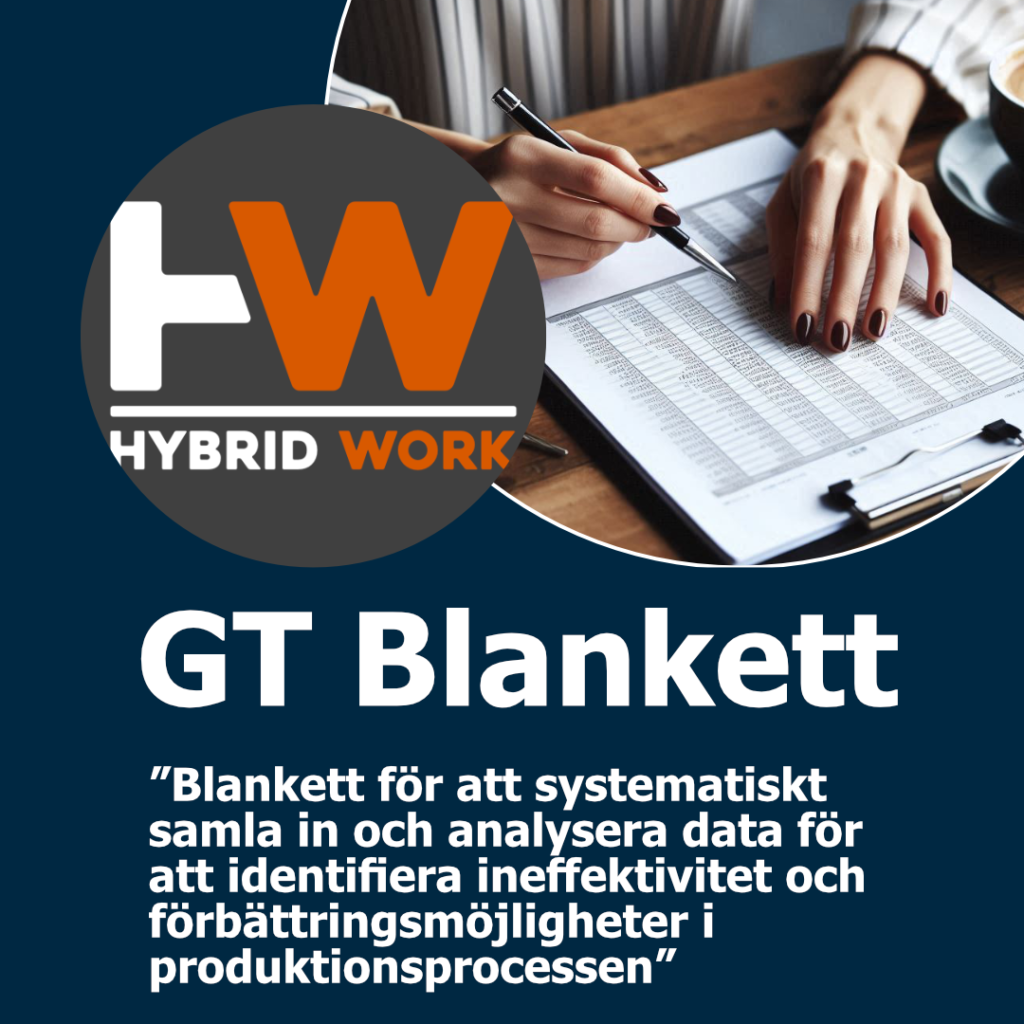
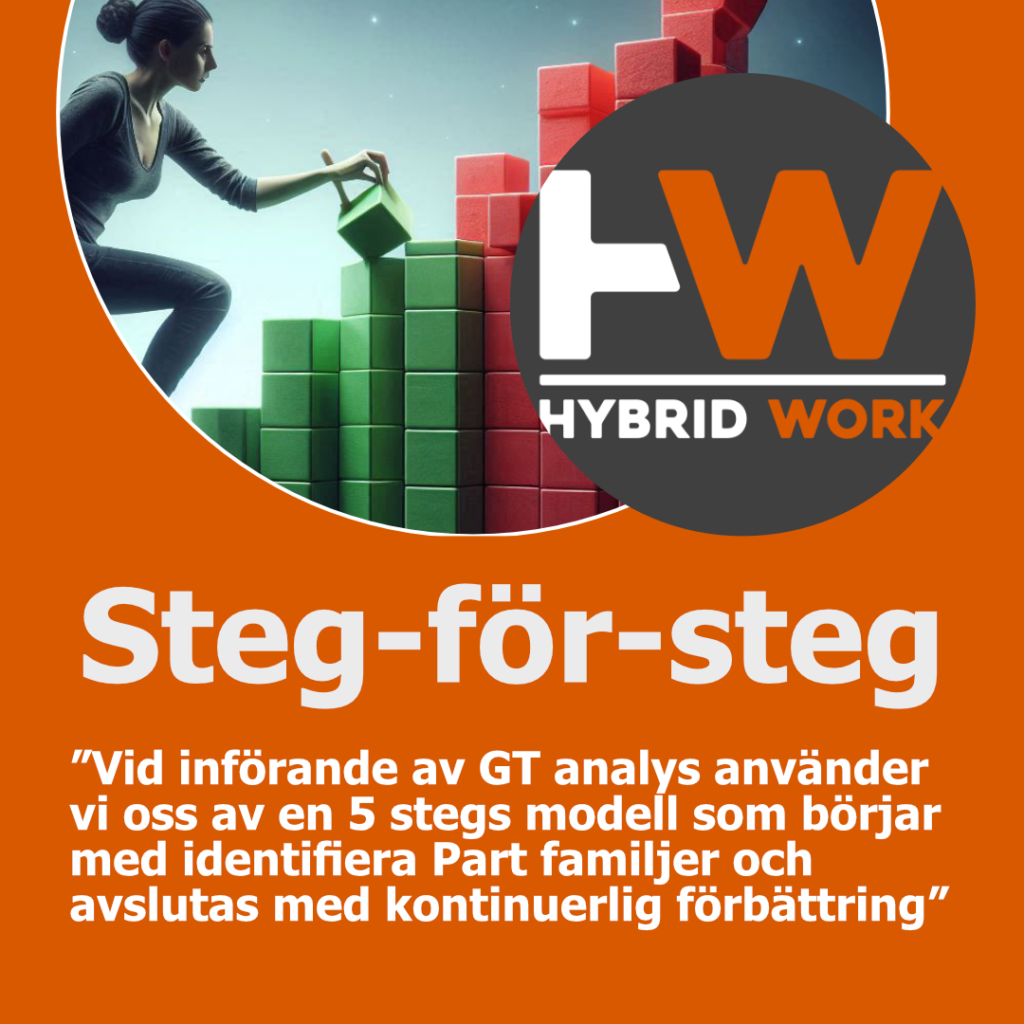
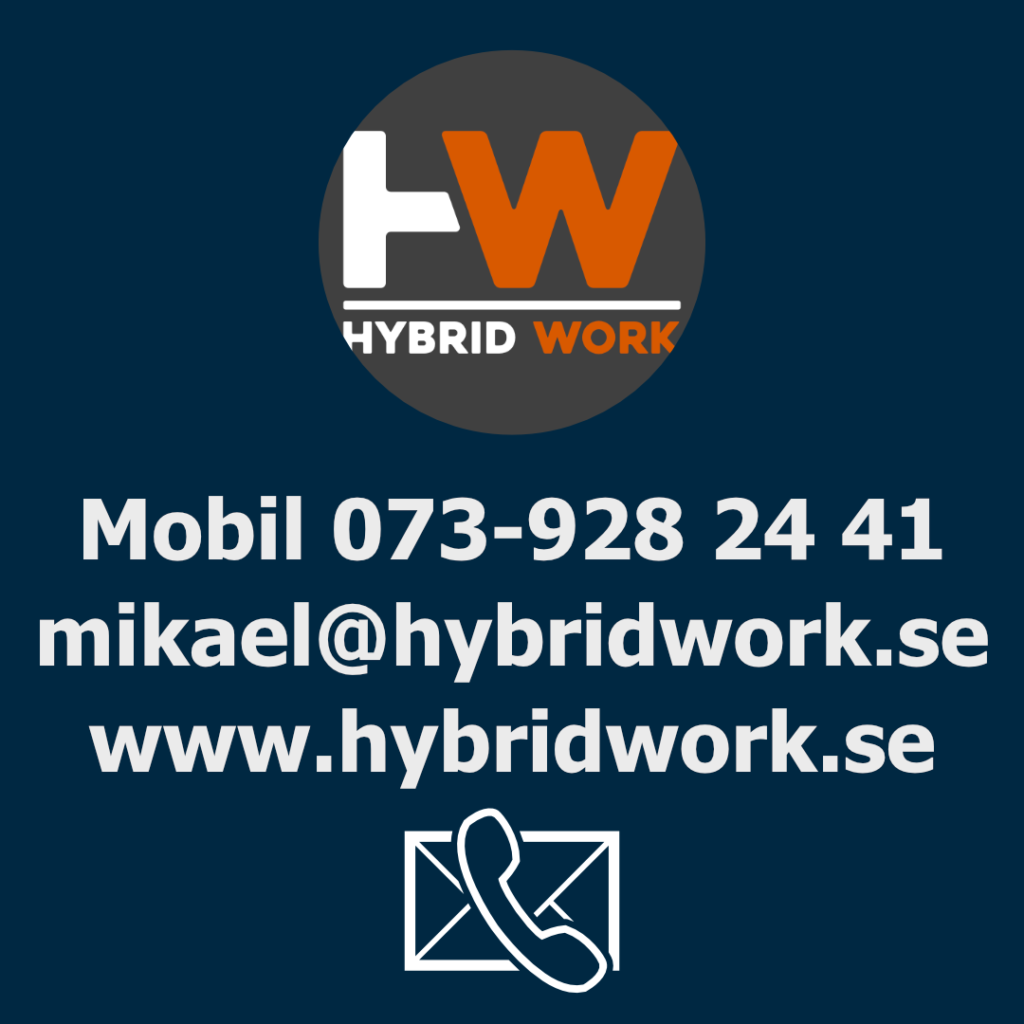
Behöver ni hjälp att komma igång med konceptet?
Vi erbjuder uppdragsbemanning ex produktionstekniker som en resurs vid genomförandet eller projektledare för bästa styrning. Planerar ni att införa flera Lean koncept, ta då in en Lean Coordinator som hjälper er med en övergripande Lean strategi.
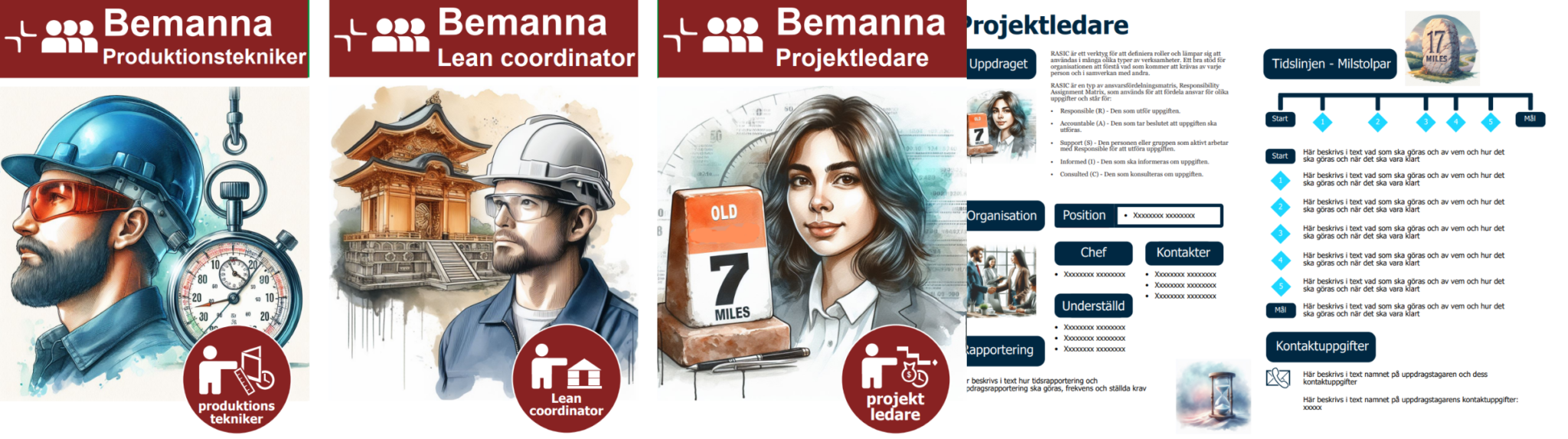
Intresserad?
Rekrytering | Bemanning | Utbildning
mikael@hybridwork.se
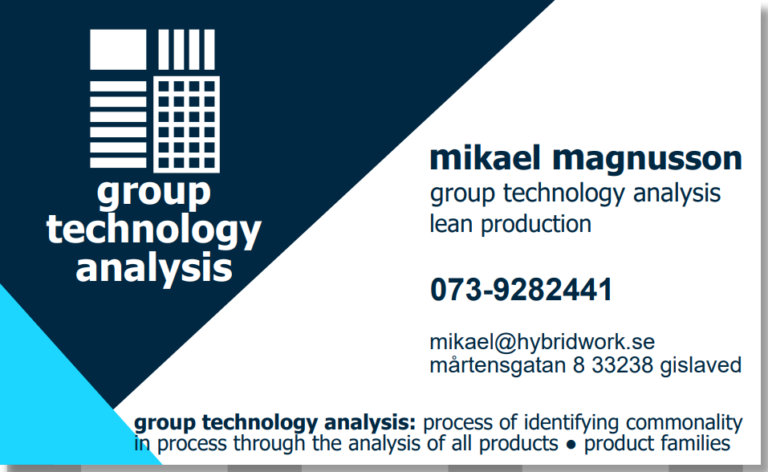
”Uppmuntra till inlärning med Green Card certifiering och säkerställ att kompetensen finns för att utföra jobbet eller konceptet – ett win-win för både företaget och för era anställda i deras karriär”
Bygger på en kompetensmatris som visar vilka aktiviteter som ska vara uppfyllda med dess status visualiserat.
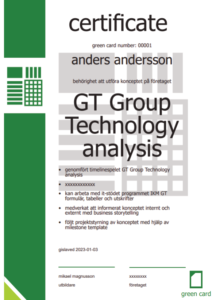
”Timelinespel, ett Gamification event. GT Group technology analysis Företagsspel för lättsamt lärande att implementera koncept. Främjar teambuilding och framdrift”
Ett spelupplägg att kunna återkomma till för nya utmaningar. Teamen tränas i att aktivt lära sig och presentera lösningar. Skapar tävlingsmoment.
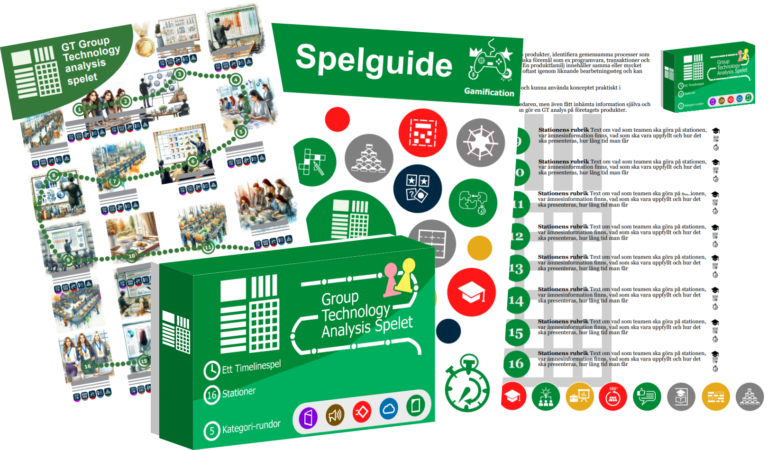
”IT stödet IKM Manager är programmoduler skräddarsytt direkt för GT Group technology analysis konceptet och stödjer ett standardiserat arbetssätt. Ger samtidigt både framdrift och historik.”
Går att företagsanpassa och vara kopplat mot affärssystem eller visualiseringsprogram ex Power Bi. Har en användarmanual som även visar hur programmet är uppbyggt.
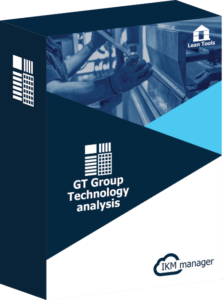
”Ge rätt förutsättning vid införandet av GT Group technology analysis konceptet med en projektplan som har tidsatta aktiviteter och en projektbudget”
Vem gör vad och när? Skapar framdrift. Göra konceptets aktiviteter i rätt tid för att kunna vara klar enligt planerat. Vi hjälper gärna er som extern projektledare.
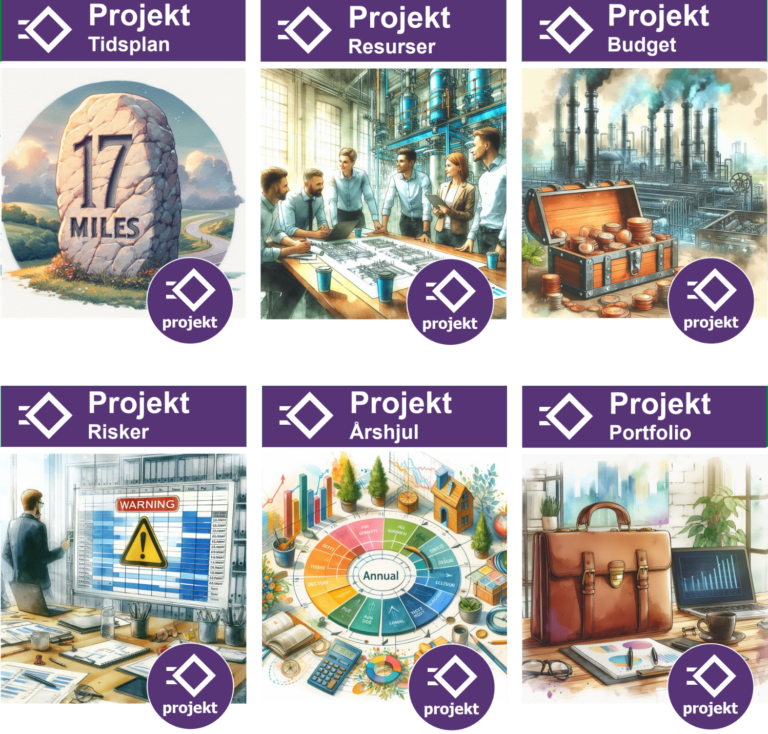
”Öka möjligheten för den nyrekryterade att lyckas i sin nya tjänst och samtidigt utveckla företaget med att föra in nya koncept – En skräddarsydd individuell Trainéeutbildning med ett schema som visar vad som ska vara uppfyllt.”
Ett trainéeprogram kan innebära att förutom traditionell inlärning och att få tillgång till mentorskap, att få göra intressanta aktiviteter som ex arbetsprover eller leda företagsspel typ våra Timelinespel.
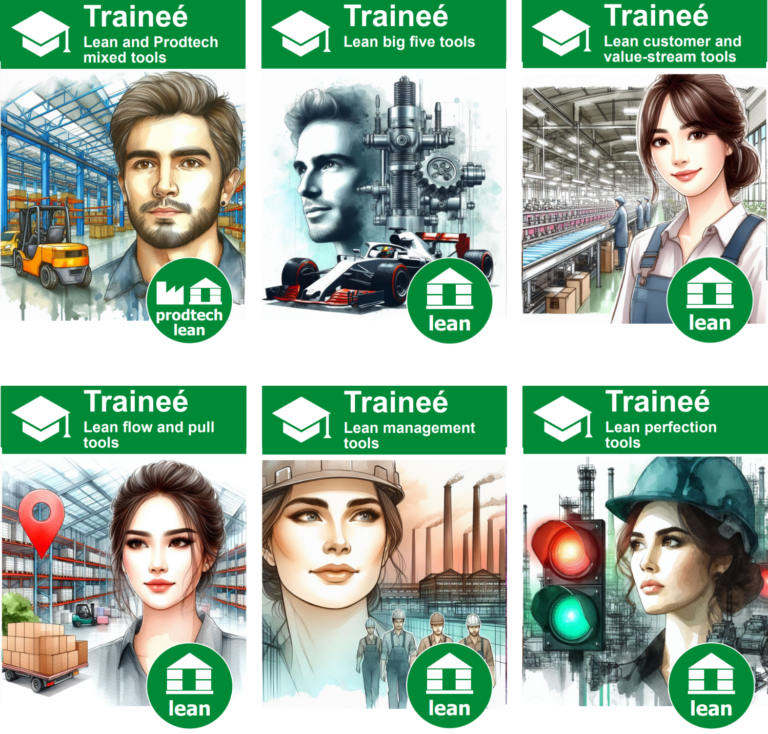